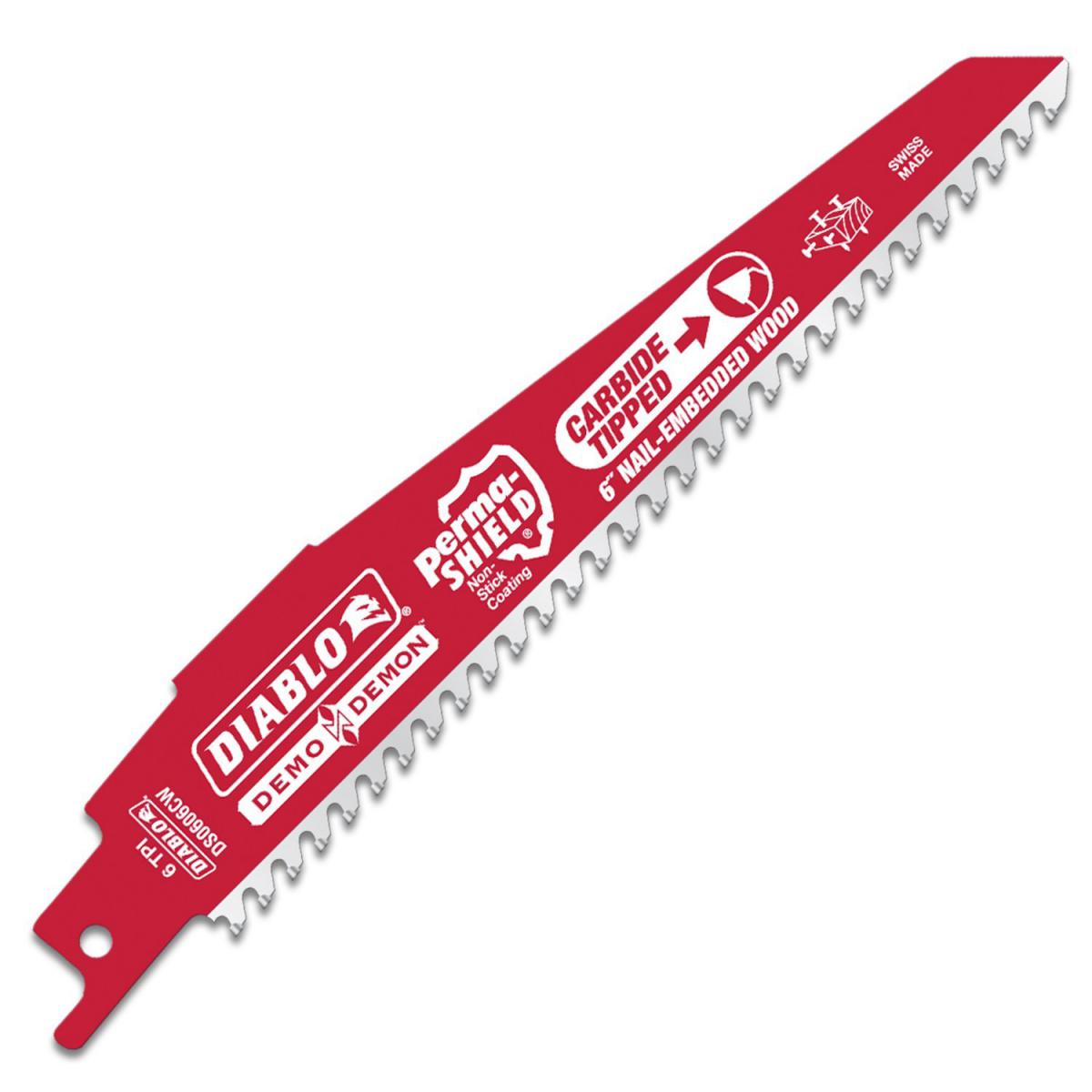
Choosing a reciprocating saw blade can be a difficult task. If you choose the wrong one, it will dull very fast and leave you without a blade in the middle of a job.If you are not careful, you'll spend a lot of time purchasing replacement blades. Let's take a look at what's important when choosing a reciprocating saw blade.
Material Type
No single reciprocating saw blade can cut every type of material. The most important thing to do is to purchase a blade that is rated for the material you want to cut. Trying to make a cut with the wrong blade will either dull and ruin the blade in only a few seconds, or make the work progress painfully slow (up to 10 times slower).
Manufacturers print large icons of the materials a blade can cut on the packaging. These icons, however, only indicate that the blade can cut a certain material, not that it is particularly good at it. Several other factors combine to determine a blade's cutting ability.
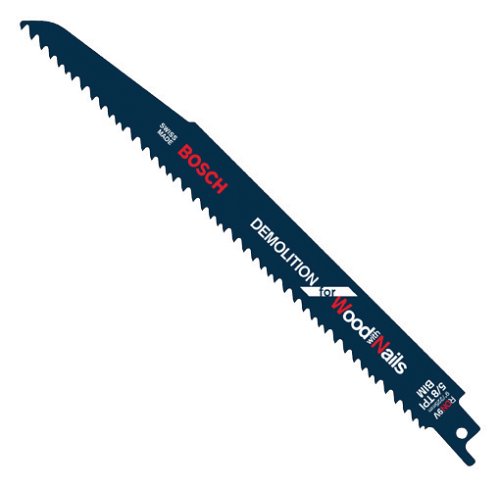
Teeth per inch (TPI)
The number of saw teeth per inch of blade primarily changes how fast the saw cuts. Blades with fewer, larger teeth cut faster than blades with a lot of small teeth. A blade with a lot of teeth, however, will leave behind much cleaner surfaces near the cut. Each tooth takes a much smaller bit out of the material. This reduces tearout and makes ridges less pronounced.
The TPI of reciprocating saw blades ranges from 3 to 18. Blades in the 3-8 TPI range are best used for making rough cuts in wood. Pruning blades often have a very low TPI. 8-14 TPI blades are capable of cutting wood and the occasional nail. Demo blades fall into this category. 14-18 TPI is the range of metal cutting and finish cut blades. The blades cut slowly, but leave being a very smooth edge.
A blade that has a different tooth density at different points along the blade is called a variable tooth blade. A 6-12TPI variable tooth blade has a 6 TPI area for fast cutting, and a 12 TPI area for fine cutting. The operator can position the blade in such a way that most of the cutting is done by the area of the blade with the optimum tooth density. A variable tooth blade can be used like two different blades without having to do a blade change.
Variable Tooth blades are not inherently better than standard blades. If you want to avoid frequent blade changes and are in hurry, a variable tooth blade is a good choice.
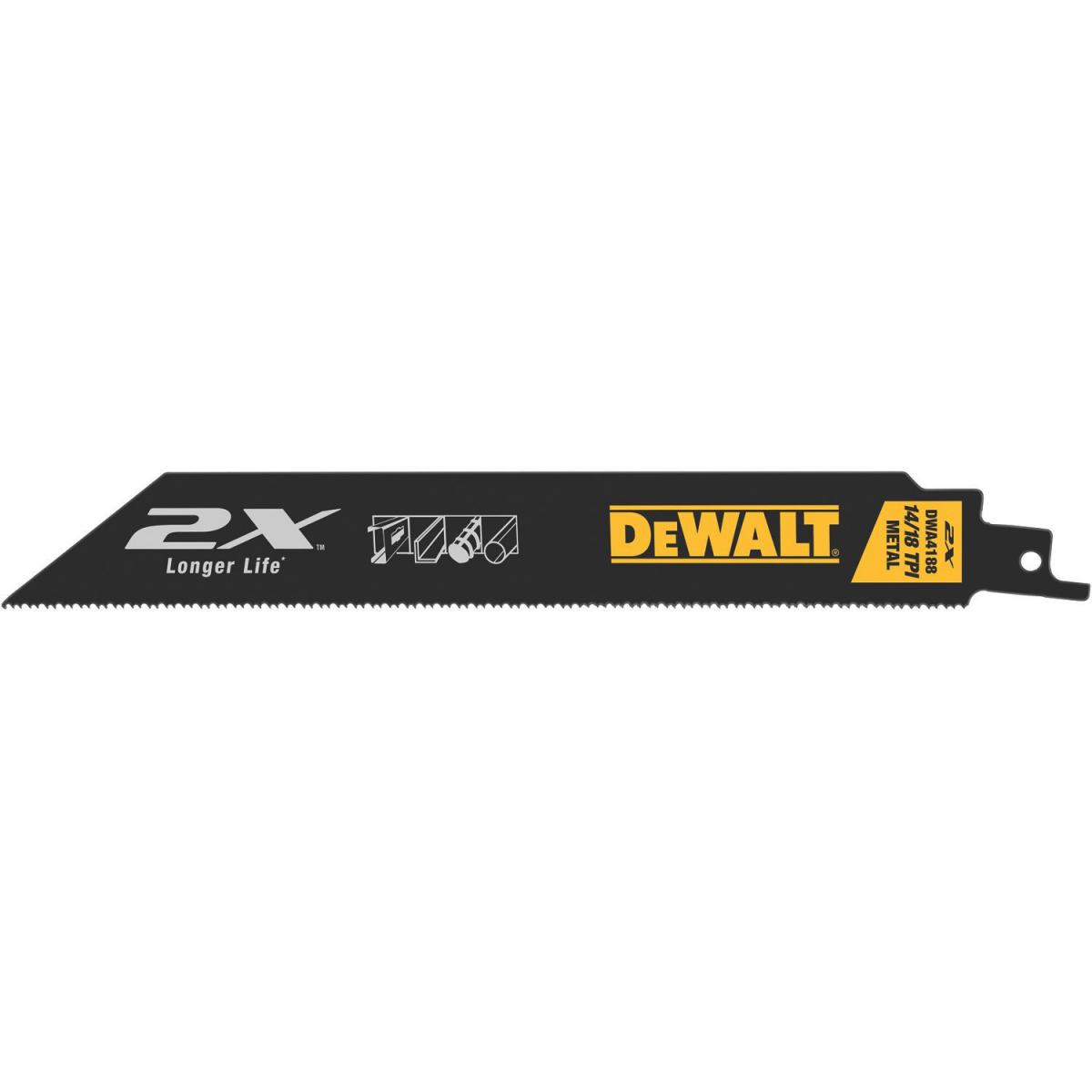
Blade Material
The material the blade is made of is a tradeoff between price and longevity. Blades made from stronger material cost more to manufacture, but last much longer. Cheaper blades are not always the better deal.
- Carbon Steel: Carbon steel blades are cheap to manufacture. They are very flexible, which makes them a good choice for getting into tight spaces. Unfortunately the teeth of a carbon steel blade are equally weak. The blade will dull very quickly, especially when cutting metal or stone. These blades are good choice for a quick job where blade longevity is not a concern.
- High speed steel: This type of steel is much stronger than the default carbon steel. Blades made from this material last up to five times longer. The teeth don't dull nearly as fast as on a carbon steel blade. High speed steel blades are more brittle than carbon blades. They do not flex well.
- Bi-metal: Bi-metal blades are made from two or more types of metal. This allows the blade to combine the best properties of both carbon steel and high speed steel in one blade. Bi-metal blades tend to last longer than the other two types. The teeth are hard, while the blade is flexible. Unfortunately the somewhat complicated manufacturing process makes these blades more expensive.
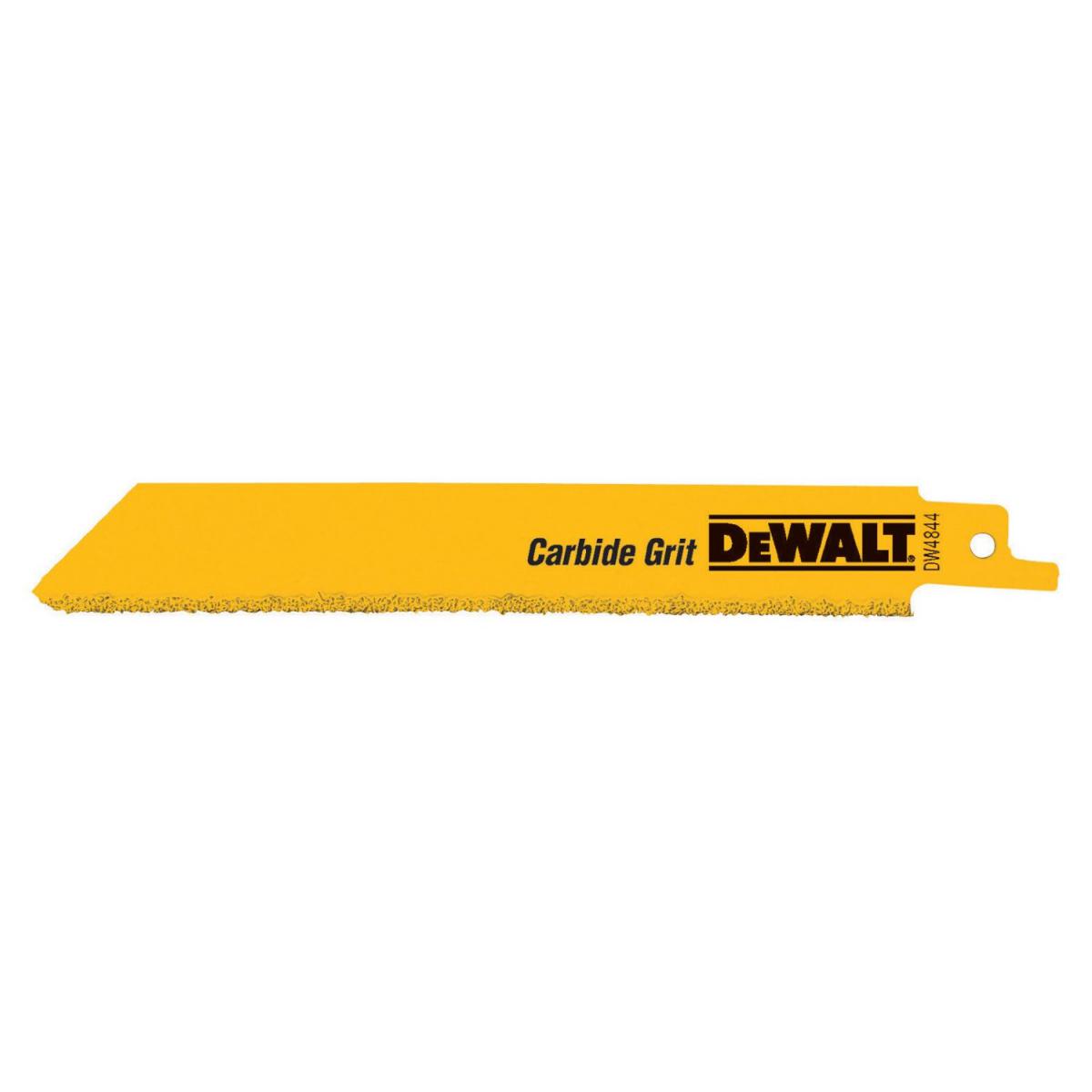
Tooth Material
The material of the cutting edge of the teeth determines much of the blades longevity and choice of material it can cut. There are several choices to consider.
Metal Teeth: The teeth on most blades are formed from the same material the blade itself is made from. This allows for fast, economic production, but does not result in the best blades. For these types of blades the choice of blade material is very important.
- Carbide teeth: Some blades bond carbide, a very hard, brittle material, to the cutting edge of each tooth. This drastically increases the cutting ability of the blade in wood and plastic. A blade of this type will last several times as long as a standard blade. Unfortunately carbide blades can only be used in wood and plastic.
- Carbide grit: This type of blade embeds small particles of carbine or industrial diamond grit along the cutting edge of the blade. This allows the blade to cut cast iron, fiberglass, cement, metal, ceramic, and clay. When used to cut wood, the blade will cut very slowly and probably start a fire.
Tooth Patterns
The pattern that is formed by the way the teeth are attached to the blade influences the speed and quality of the cut. There are two common tooth patterns.
- Wavy Set: On a wavy set blade the teeth form a wave along the cutting edge of the blade. Each individual tooth does not extend beyond the width of the blade shaft. This type of blade produces a finer cut at the expense of cutting speed.
- Raker Set: The teeth in this pattern extend beyond the edge of the blade in an alternating fashion. This allows each tooth to make a more aggressive, but rougher cut. This type of blade cuts faster, but produces tearout and leaves a rough finish.
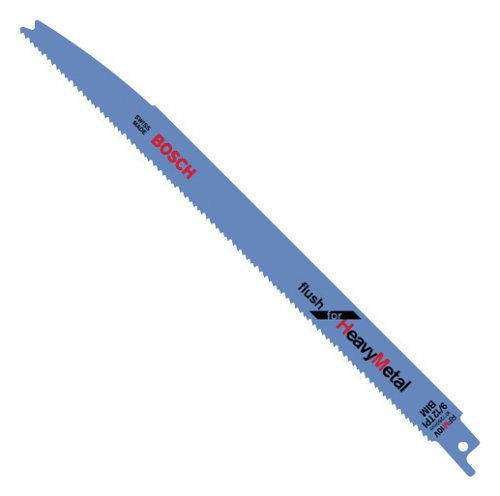
Blade Length
The blade length determines the maximum length of cut that can be made with the blade. Pruning blades, for example, are long blades. This allows the arborist to remove large branches from trees without having to make a plunge cut. Metal blades for plumbing are relatively short. Cooper lines are rarely larger than 1". The short, rigid blade excels at making the straight, clean cuts that are needed for a watertight joint.
The longer a blade gets, the easier it becomes to bend the blade during a cut. A short blade creates a cleaner, more square and true cut than a longer blade. Attempting a plunge cut with a long blade almost always ends with a bent blade.
Blade Thickness
The blade thickness determines how well the blade resists bending. Blades made for critical applications are thicker. These blades will leave a square cut and won't quit before the cut is complete.
Economic blades are as thin as possible in order to keep costs down. Ideally the blade resists bending only as long as teeth on the blade keep cutting. Any extra rigidity is wasted material and money. If used carefully a thin blade can save money.
Most general duty blades are about 0.03" thick. Heavy duty blades come it at double that, or about 0.06".
The best Goto-Blade
If you do not want to worry about all these factors, a general purpose blade with be your best option. These blades try to offer good cutting performance in as wide a range of materials and situations as possible.
Our favorite is the Bosch RDN9V 9-inch 5/8T blade. Technically a demolition blade, Bosch has created a solid performer as a reasonable price. This blade will cut through wood without trouble, and perform decently in metal. I keep a pack or two in my saw case. More often than not the Bosch RDN9V is the best blade in my arsenal for the job at hand.
Summary
You can save yourself a lot time by choosing the correct blade for your reciprocating saw. Choosing a blade rated for the material you want to cut is paramount. If you do just that you will get decent performance and longevity out of your blade.
If you want to pick a blade that will get the project done the fastest while lasting the longest, you have to pay attention to the blade material, TPI, tooth material, blade length, and blade thickness. Take the time to study the market the first time around. Soon you'll have your set of goto-blades you'll use on every project.
(R5FZQ43AN86S)